There are two starting points, depending on your preference of whether you want to stir in a batch or flow something though a tube. If you plan to use large scale up reactors, then batch stir methods are great, but if you imagine wanting to flow material through a ‘cleaning’ column, then the SPE quick test works well.
I’ll cover both methods in this series, but let’s first consider the flow kit, it contains 5 top performing metal scavengers, pre-packed into 1g SPE tubes, ready to accept samples.Precious metals such as Pd, Pt, Ru and Rh in organometallic catalysts are becoming more widespread in industrial synthesis.
So how do we actually do metal scavenging?
Achieving purity levels for metal contamination is becoming increasingly challenging, irrespective of actual legislative limits, processes need to be robust enough to accommodate slight variation in inputs, such that limits of 5 ppm (ingested), and 1 ppm (parenteral) API now the benchmarked standard. In our work, we chose to target Pd, but this works for other metals and also mixtures of metals.
First step, lets apply our contaminated API solution. In our example we purchased 2-methyl-5-phenyl benzoxazole from a standard chemical supplier and manually spiked this with Pd catalyst, to the tune of 500ppm Pd (which is a typical residual level after 0.5-1 mol% Pd catalysed reactions). We used a classic palladium dichlorobis-diphenylphosphine catalyst and dissolved this up in THF, with a small % of DMF to increase solubility.
The rest of the process was then quite simple, taking a few minutes in the lab.
- Split stock solution 5 ways
- Add a portion to each SPE cartridge in the kit
- Assess the results…….
This is what some of the tubes looked like. The palladium often changes colour when being fixed on a ligand in the process of metal scavenging.
We took portions of the stock solution which contained 1g of the 2-methyl-5-phenyl benzoxazole in a palladium solution of 500ppm, and applied them to the metal scavenger tubes. It is good practice to wet the tubes first with a few column volumes of solvent, this simply removes air spaces within the scavenger bed, to eliminate any ill effect from channelling. In very large packed bed, it is not always necessary to do, as there is good contact and residence time.
So, we measured both the mass recovery of our 1g organic molecule and also the reduction in concentration of Pd. In line with ICH guidelines and industry practice, we simply sent our samples for external analysis from a professionally accredited testing lab running standard ICP analysis methods.
As you can see, there was a difference in scavenger capability, so our screening test was successful. The purpose of a screening test is to eliminate a bad candidate, as that will save a lot of time and analytical developmental resource later. Here is a summary of our findings:
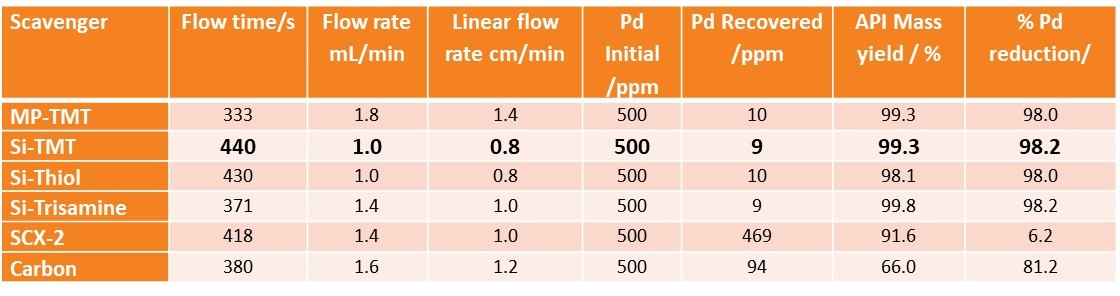
- We eliminated SCX-2 and carbon, carbon yield was far too low, and the basic product meant that the acidic scavenger SCX-2 was not a good choice for this application.
- Knowing this, and since we were looking for the most robust SOP to move forward, we also parked Si-Trisamine, as it is basic, and could potentially interact with acidic APIs, in future.
So Si-Thiol, MP-TMT and Si-TMT remain and we chose Si-TMT based on all round technical performance.
Now we’ve identified a metal scavenger, how do we scale up?