For most organic and medicinal chemists flash chromatography is just another step in the synthesis work flow - react, analyze, purify, react, analyze, purify... until the final product is made. The desired product of each reaction, and the mixture of other species present are, of course, different with each cycle. Separating the desired compound efficiently without a lot of hassle is something I have written about in this post as well as in others in this series.
In this post, I've written about how that TLC (thin layer chromatography) plate you use for monitoring your reaction can be used to create reliable, efficient, effective gradients.
In previous posts I wrote about how solvent choices and their ratios impact purification by flash chromatography. Obtaining a separation of your target product from its by-products and starting materials is critical; getting your product fully resolved from the other components is just as important.
With the advent of automated gradient flash chromatography at the turn of the century, flash chromatography has become more mainstream in synthesis labs. No longer are chemists relegated to isocratic elution on glass columns with manual fraction collection. Now all you need to do is run a TLC plate or two, enter data into the flash system's software, and a gradient is created tailored to your sample. Some flash systems even calculate sample load and suggest a cartridge or column that has the correct capacity for the predicted load, a major time saving capability. No more guessing on solvent ratios, gradient shape and duration, or load size - it is all done for you!
So how does this work? Well, most flash system manufacturers have created their own unique algorithms to address the conversion of TLC Rf data to an "optimized" gradient. Some require one TLC plate while others require at least two.
In the simplest form, a TLC to gradient algorithm will be based on the amount of strong solvent used with the TLC. Biotage, for example, uses the following as its linear gradient algorithm.
Gradient segment 1: 1/4 of the TLC strong solvent % for 1 CV
Gradient segment 2: 1/4 of the TLC strong solvent % to 2x the TLC strong solvent % over 10 CV
Gradient segment 3: Hold 2x the TLC strong solvent % for 2 CV
This algorithm ensures each compound with Rf values from 0.1 and higher are eluted in the defined 13 CV gradient. This algorithm also determines and suggests a load size per cartridge based on the entered Rf values, Figures 1 and 2.
Figure 1. TLC to gradient software being used to create a linear gradient and estimate sample loading and cartridge size.
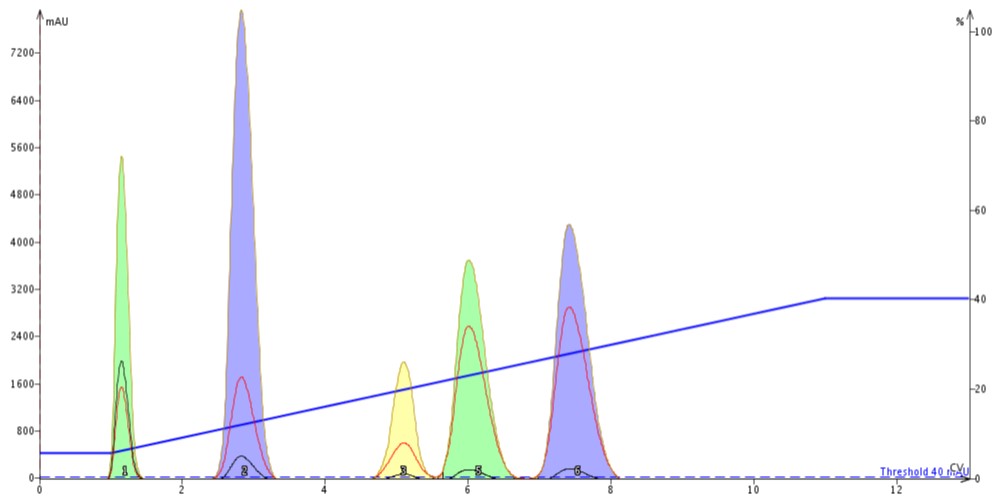
Figure 2. Linear gradient results created from TLC data above; 100 mg sample load on a 10g cartridge.
Another elution option is the step-gradient. Like the linear gradient, step-gradients can be developed using the same TLC data (strong solvent % and compound Rf values) but can be more challenging to optimize without a good algorithm, Figure 3. Step gradients are very beneficial, especially if you do not know which compound is your product. With a well designed step gradient you can optimize the gradient around multiple compounds in the mix, Figure 4.
Figure 3. Accurate step gradients can be developed using as few as 2 TLC plates worth of data and a well-designed algorithm.
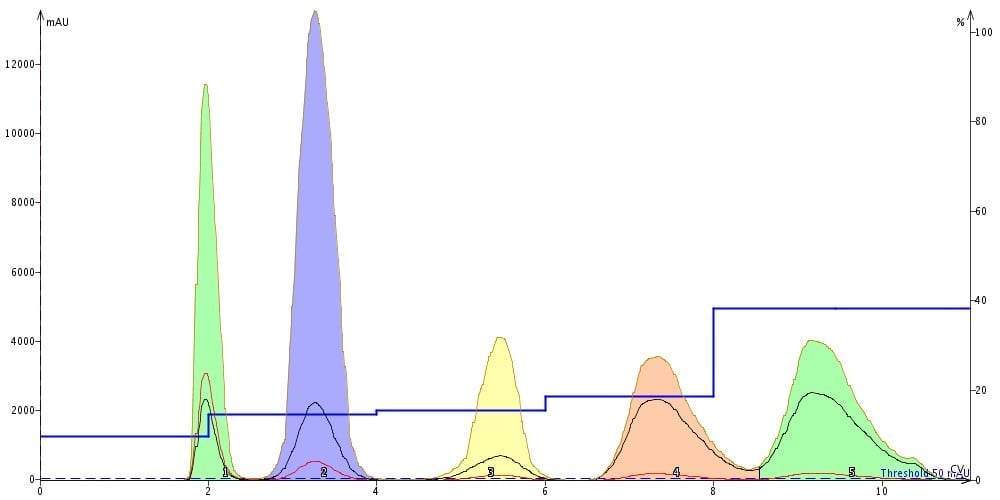
Figure 4. Resulting step gradient separation from above method shows complete resolution of each compound using a 10 g silica cartridge.
Some other flash system manufactures' algorithms focus on eluting the compound of interest in a specific number of CV or require two plates and generate a 2-part linear gradient with an isocratic hold around the target product's average Rf. Both of these algorithms create gradients but neither determine load size.
The choice of which gradient type to use is up to you, each will work when you use the right algorithm and follow loading guidelines. Linear gradients are simple and efficient but typically consume more solvent than a step gradient and have been shown to have lower loading capacity than step gradient methods. Step gradients use less solvent and may improve load capacity on the same size cartridge but can be challenging to optimize.
For more information on flash chromatography, download our white paper Successful Flash Chromatography.